|
Антон_Росляков
Воскресенье, 01 Октября 2023 г. 06:38 (ссылка)
Самая частая проблема при сварке инвертором, это залипание электрода. В статье мастер сварщик расскажет, почему прилипает электрод при сварке инвертором, и как собственно бороться с этой напастью.
Причины залипания электродов
Чаще всего с этой проблемой сталкиваются сварщики, использующие в своей работе трансформаторы без возможности точно настроить режим работы, или новички, использующие инверторы. В дорогих моделях современных инверторных аппаратов есть функция «Антизалипания», предотвращающая залипание электрода. Но начинающие сварщики часто приобретают бюджетные модели и из-за отсутствия опыта сразу же сталкиваются с залипанием.
Проблемы с расходным материалом;
Неправильная первоначальная настройка используемого аппарата и нестабильность электрической сети;
Низкая квалификация пользователя.
К первой категории относятся следующие причины:
Вторая категория объединяет следующий комплекс причин:
Перепады подаваемого напряжения (результатом становиться изменение параметров сварочного тока: его пониженное значение или резкое изменение);
Не правильное подключение контактов;
Сбой первичных настроек аппарата;
Нарушение целостности кабеля (излом, нарушение оплётки);
Изначально сварочный аппарат настроен не правильно.
К субъективным причинам относятся:
Многообразие причин того, что расходник липнет к металлу, требует тщательной подготовки. Любая причина может привести к целому ряду негативных последствий. Залипание электрода произойти на этапе образования сварочной дуги, во время сварки. Любой способ сварки может привести к прилипанию, в том числе инверторный.
Повышенная влажность электрода
Состав так называемой обмазки, имеет пористую структуру, состоящую из мелкого порошка. От её качества зависит появление прилипания. Она имеет свойство постепенно накапливать влагу, даже при нахождении в помещении с естественной влажностью.
Применение расходника без предварительной просушки приводит к негативным последствиям, электрод залипает при сварке. Особенно этот эффект проявляется в тот момент, когда производится розжиг дуги. Прилипание может быть настолько прочным, что приводит к разрушению расходника и деформации стыка свариваемой детали.
Для устранения этой проблемы профессионалы рекомендуют использовать специальные приёмы для удаления избыточной влажности.
Целесообразно хранить открытые пакеты с расходниками, которые остались от предыдущей сварки в специальном термопенале. Перед употреблением необходимо их поместить в сушильный шкаф. Перед проведением сварки следует проверить слипание кончика электрода на сторонней поверхности.
Низкое качество электродов
На прилипание электродов влияет их низкое качество. Современные производители предлагают большое количество различных видов таких изделий. Каждый из них предназначен для решения конкретных задач.
Большой ассортимент привел к негативному явлению, которое подталкивает производителя к наращиванию темпов производства с постепенным снижением качества своей продукции. Этот процесс наблюдается даже у хорошо зарекомендовавших себя на рынке производителей. Опытные сварщики замечали, что качество электродов в начале выпуска новой партии значительно выше, чем у последующих экземпляров. Вторым неприятным моментом является подделка изделий известных производителей.
Такие фирмы вообще не следят за технологическим процессом. Мелкие компании, работающие на рынке не всегда способны точно отслеживать технологию производства, что приводит к появлению некачественной продукции. Именно они обладают способностью прилипать в самый неподходящий момент. При покупке новых расходников необходимо тщательно осмотреть их внешний вид.
Неправильные настройки аппарата
Субъективным фактором, способствующим проявлению этого эффекта, является неправильная предварительная настройка сварочного аппарата.
Прежде чем взять в руки держак с электродом, следует почитать более подробно о процессе дуговой сварки. Здесь важно учитывать толщину свариваемого металла, от которого зависит диаметр электрода и сила тока для нормальной работы сварочным аппаратом. Если сила тока будет выставлена на инверторе слишком маленького значения, то получить стабильную дугу не удастся, она все время будет тухнуть, а электрод, соответственно, прилипать к поверхности металла.
Неочищенная поверхность заготовки
Предварительная подготовка деталей перед проведением сварки предполагает обработку поверхности, направленную на удаления различных видов загрязнения. Это необходимо для последующего получения качественного шва и предотвращения прилипания.
Для решения данной задачи применяют различные способы: механический, химический, термический, электромагнитный. Наиболее дешёвыми и распространёнными являются механические способы очистки поверхности.
В этих методах используются различные инструменты и абразивные материалы. Чтобы электрод перестал прилипать при проведении сварочных действий, необходимо выбрать метод обработки поверхности и тщательно провести необходимые операции.
Нестабильные параметры электросети и тока
Часто они могут липнуть из-за нестабильных параметров электрической сети, к которой подключён сварочный аппарат. Особенно этот эффект проявляется при снижении напряжения питающей сети ниже номинального или периодического колебания этого параметра. Для устранения такого недостатка целесообразно применять электронные устройства стабилизации напряжения.
Низкая квалификация сварщика
Важным субъективным фактором, приводящим к низким результатам получаемого шва, является слабая квалификация сварщика. Слабая теоретическая подготовка и недостаточный опыт позволяет периодически залипать электрод во время его контакта с заготовкой. Проводимая сварка таким специалистом может привести к получению шва низкого качества и порче самой детали.
Как предотвратить прилипание электрода
Теперь, когда мы выяснили, почему залипает электрод при сварке инвертором, мы расскажем о простых методах предотвращения ошибок. Что может сделать каждый сварщик, чтобы не прилипал электрод? Решение нетрудно найти исходя из сути проблемы.
Как правильно разжигать дугу
Ошибки во время розжига электрода, как правило, допускаются в самом начале своей карьеры, начинающими сварщиками. Электрод просто касается металла и не убирается вовремя от него, так и залипая на одном месте. Чтобы избежать подобной ошибки следует стукнуть электродом по заготовке, и тут же отвести его вверх, но не слишком высоко, чтобы дуга не погасла. В дальнейшем, с приходом опыта, данное действо будет происходить на полном автоматизме.
Слишком короткая дуга, также становится причиной залипания электрода при сварке инвертором. Многие опытные сварщики рекомендуют учиться варить инвертором на короткой дуге, порядка 3-4 мм. Меньшая дуга приведёт к залипанию электрода.
Электроды для сварки инвертором
Принято считать, что есть специальный вид электродов, которые используются для сварки инверторными автоматами. Но это не так, для варки инверторами можно использовать полный перечень в номенклатуре электродов, но среди них есть те, которые рекомендованы к сварке высокочастотными инвекционными токами.
Выбор качественных и правильных расходных материалов – это залог успешного проведения сварочных работ. Самым первым параметром, по которому выбираются электроды – это их диаметр. Нормативные документы содержат полную информацию в каталогах, где указан диаметр электрода для каждой марки стали.
Стоит знать, что толщина шлаковой обмазки электрода не входит в расчетные параметры диаметра самого стержня электрода. Диаметр обмазки – параметр, который индивидуален для каждого вида электродов.
Все электроды маркируются одной из четырех букв, которые обозначают толщину обмазочного покрытия из шлака или силикатов:
“М”, это значит, – 1,2 мм. – толщина обмазки для электродов с такой маркировкой. Кроме того буква “М” означает то, что электрод покрыт оксидами;
“С” – толщина покрытия составляет 1,4 мм. Средняя толщина обсыпочного покрытия;
“Д” – толщина составляет 1,6 мм;
“ОС” – электроды с особо толстой обсыпочной частью, которая составляет 1,8 мм.
Необходимо отметить, что электроды иностранного производства маркируются аналогично, но в некоторых случая диаметр внутреннего стержня с обмазкой учитываются суммарно.
Для осуществления правильного подбора применительно к свариваемому металлу и чтобы избежать залипания электродов, нужно знать какие из них наиболее соответствуют соединяемым заготовкам. Технические характеристики покрытия и рекомендуемые для сварки металлы и сплавы соответствуют разным маркам электродов, а именно:
Для работы с конструкционными низколегированными, углеродистыми сталями необходимо использовать УОНИ-13/55, ОМА-2, ОЗС-30, МР-3М, Ви-10-6, АНО-21 и ВСФ-65У;
Легированные высокопрочные стали варят ЭА-981/15, ЭА-395/9, НИАТ-5, ОЗШ-1 и НИАТ-3М;
Для теплоустойчивых и жаропрочных сталей используют АНЖР-2, ТМЛ-3У, ЦЛ-39, ИМЕТ-10, КТИ-7А и ОЗЛ-35;
Нержавеющие и коррозионностойкие сплавы сваривают с помощью НЖ-13С, НИАТ-1, УОНИ-13НЖ, ЦТ-15, и ЭА-400/10Т;
Разнородные сплавы и стали варят ЭА-391/15, ЦТ-28, ОЗЛ-32, АНЖР-2, НИИ-48Г, ИМЕТ-10, В-56У и ВИ-ИМ-1;
Для спецсталей подходят ОЗЛ-44, АНВ-20, ЭА-112/15 и НИИ48Г;
Чугун варится с помощью ОЗЖН-1, ОЗЧ-2, МНЧ-2, ЦЧ-4;
Для алюминиевых сплавов нужны ОЗА-2, ОЗАНА-2, ОЗА-1 и ОЗАНА-1;
Медь и её сплавы хорошо варятся АНЦ/ОЗМ-2, ОЗБ-2М (бронза), Комсомолец-100, ОЗБ-3;
Для никеля и сплавов используют В-56У, ОЗЛ-32;
Резку металла проводят АНР-2М, ОЗР-2, ОЗР-1.
Согласовав металл заготовки с маркой электрода, вы, скорее всего, сможете избежать залипания при работе с инверторными аппаратами.
Какой ток выставить на инверторе
Неправильно выставлен ток на инверторе — прежде чем приступить к сварке, следует разобраться с тем, какой должен быть выставлен ток на инверторе, для работы с теми или иными электродами, металлом и т. д. Многое здесь зависит, конечно же, от диаметра электродов и от толщины свариваемого металла. Однако неправильно подобранный ток сварочного инвертора, как раз и приводит к прилипанию электрода.
Так, для сварки инвертором, применимы следующие значения тока:
При работе с электродами 2 мм — минимальный ток 40А, а максимальный ток 80А;
Для работы с электродами 3 мм, сварочный ток должен быть в пределах от 80 до 120А;
Чтобы варить электродом 4 мм, ток должен быть выставлен на инверторе в пределах 120-160 А.
Современные сварочные инверторы имеют плавную регулировку тока. Поэтому очень просто при залипании электрода подрегулировать сварочный ток в большую сторону, а при прожиге металла, наоборот.
Теперь вы знаете, как правильно варить электросваркой, чтобы электрод не прилипал к металлу и ваши труды не были напрасны. Кратко резюмируя, следите за выставленными параметрами тока на вашем инверторе, не экономьте на качественных электродах и учитесь правильно поджигать дугу.
Антон_Росляков
Среда, 21 Сентября 2023 г. 00:44 (ссылка)
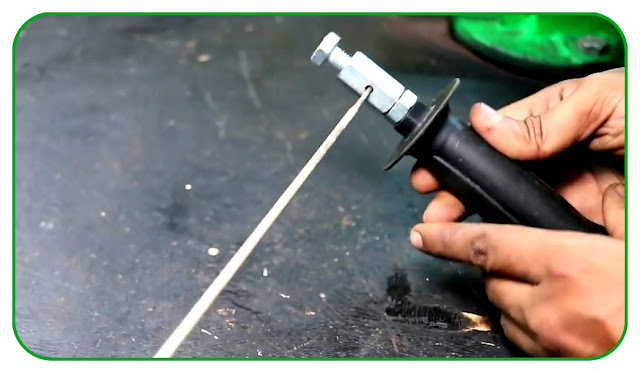
Жесткая фиксация электрода очень важна, особенно, если в хозяйских делах пришлось взять в руки сварочный аппарат. У мастера сантехника с надежностью фиксации проблем обычно не бывает, а вот у любителей дела могли бы обстоять и лучше. Именно поэтому стоит взять на вооружение один способ создания держателя.
Материалы и инструменты
Для того, чтобы собрать простой, но надежный держатель для электрода, понадобится шпилька 70 мм с резьбой на 12, а также болт 35 мм. Кроме этого нужно раздобыть пластиковый держатель, стяжную гайку, удлиненную гайку 25-30 мм, а еще понадобится две обычные гайки. Если все это есть – можно приниматься за работу.
Рабочий процесс
Берем подготовленную удлиненную гайку и размечаем на ней центр, после чего сразу же заживаем ее в тисках. Используя обыкновенную дрель, проделываем по разметке сквозное отверстие. Следует помнить, что его диаметр должен быть примерно на треть больше толщины используемого электрода, для которого и делается держатель. Обязательно следим за тем, чтобы сверло шло перпендикулярно.
Берем болт и зажимаем его в тисках. Вооружившись болгаркой, срезаем у него шляпку. На ее место привариваем стяжную барашковую гайку. Учитывайте тот факт, что длина свободной резьбы конструкции не должна оказаться меньше, чем отрезок от центра отверстия до края длинной гайки.
Теперь понадобится найти старую нерабочую болгарку и снять с нее ручку. Избавляемся от имевшегося в ней болта и рассверливаем имеющееся отверстие под шпильку. Теперь остается только собрать все заготовленные части конструкции и сделать намотку провода. Самое главное здесь в том, что шпилька будет помещаться внутрь рукоятки и окончательно фиксироваться при помощи двойной гайки.
Вот, как выглядит конечный результат
Видео
В сюжете - Как сделать держатель для электрода
В продолжение темы посмотрите также наш обзор Как выбрать сварочную маску хамелеон
Источник
https://santekhnik-moskva.blogspot.com/2019/08/Kak...-derzhatel-dlya-elektroda.html
https://tvin270584.livejournal.com/1237789.html
https://dzen.ru/media/masteronlayn/vyzov-svarscika...ngrad-650b5e254137e13b853f8f29
https://santekhnik-moskva.mirtesen.ru/blog/4335912...aliningrad-Svarochnyie-rabotyi
Антон_Росляков
Понедельник, 18 Сентября 2023 г. 12:16 (ссылка)

Начинающие сварщики часто задаются вопросом: «Зачем вообще нужны другие комплектующие, если есть полуавтомат, выполняющий быструю и качественную сварку с помощью обычной проволоки и газа?». Да, для любительской и профессиональной сварки часто используют полуавтоматическое сварочное оборудование. В таких аппаратах проволока подается непрерывно, поэтому швы получаются прочными и долговечными. Нет необходимости постоянно менять электрод, если нужно сварить длинный шов или наплавить много металла. При этом качество сварочных работ на голову выше, чем работа с электродами. Однако, есть одно «но».
Сварка с помощью полуавтомата требует наличия газового баллона, вес которого достигает 80 килограмм. Если вы работаете на улице или вынуждены постоянно перемещаться с места на место во время сварки, то связка полуавтомат + газовый баллон значительно усложняет задачу. Эта проблема решается с помощью газового шланга, но он стоит недешево. Альтернативой является порошковая сварка (FCAW), имитирующая работу в среде защитных газов, при этом газовый баллон не требуется. В статье мастер сантехник расскажет, что это, как это работает, и каковы преимущества и недостатки сварки порошковыми проволокой.
Основные характеристики проволоки порошкового типа
Сварка порошковой самозащитной проволокой — это способ механизированной сварки, при котором защита и легирование металла шва производится за счет шихты, помещенной в самой проволоке, состоящей из стальной оболочки и неметаллического сердечника.
Входящие в состав сердечника проволок компоненты при нагреве в сварочной дуге создают необходимую шлаковую и газовую защиту расплавленного металла. Порошковые проволоки позволяют в широких пределах варьировать своим составом и свойствами, ввиду чего сфера их применения практически не имеет ограничений.
Сварка самозащитной порошковой проволокой востребована в труднодоступных местах. Это могут быть высотные работы или в тоннелях под землей. Небольшой полуавтомат можно повесить на плече, а для выполнения сварки необходима только розетка с 220V. Благодаря такой компактности эта технология широко применяется на строительных площадках и монтажных работах. Сборка и сварка металлических конструкций таким способом производится очень быстро.
Проволока широко используется благодаря разнообразию диаметров, минимальное значение которого начинается от 0,8 мм и заканчивается на 2,4 мм. Это позволяет сваривать как тонкие листы стали, с толщиной стенки 1,2 мм, так и толстые стороны до 7-10 мм. Этим способом можно работать с углеродистой сталью, оцинкованным железом и нержавейкой. Для этого важно правильно выбирать материал самой проволоки и вид внутреннего наполнителя.
Преимущества и недостатки порошковой проволоки
Сварочный процесс с использованием непрерывной подачи самозащитной проволоки отличается несколькими достоинствами:
Нет необходимости в баллоне с газом;
Легкая транспортировка оборудования на рабочее место;
Возможность производить сварку в труднодоступных местах (на крыше, в тоннеле);
Высокая скорость работ по сравнению с покрытыми электродами;
Малая чувствительность дуги к ветру и сквознякам.
Но этот вид сварки имеет и недостатки. Один из них — высокая стоимость расходных элементов. Покупать ее ради экономии на газе не стоит. Оправдывает себя самозащитная проволока только в труднодоступных местах. Еще одним недостатком является плохое качество швов по сравнению с полуавтоматом, которым варили в среде инертного газа. Не годится этот вид сварки и для соединения труб под давление.
Подробные сведения о составе порошковых проволок
Проволока с собственной защитой изготавливается уже более полувека, а впервые она была выпущена на заводе, принадлежащем фирме "Линкольн Электрик".
Проволока для полуавтомата состоит из:
Специального наполнителя (его называют сердечником);
Оболочки.
Под оболочкой понимают ленту (холоднокатаную), изготовленную из мягкой неполированной стали с малым содержанием углерода. По ширине и толщине такая лента может иметь различные размеры, которые устанавливаются тем, какой диаметр должен быть у готовой оболочки. Как правило, толщина ленты находится в пределах 0,2–0,8 миллиметров. Поставляют интересующую нас ленту в кругах либо рулонах, причем сверху на материал наносится консервационный смазочный состав, который затем снимают (удаляя попутно все загрязнения) ультразвуковым или механическим способом.
Сердечник проволоки – это комбинация разнообразных ферросплавов, руд, минералов, металлов и иных элементов, которые обеспечивают получение швов с заданными эксплуатационными параметрами, а также устойчивое и стабильное осуществление сварочной (наплавочной) процедуры.
Все элементы, входящие в сердечник, подразделяют на следующие виды добавок:
Раскисляющие. Под такими компонентами понимают металлы с повышенным сродством к кислороду (то есть активные), которые вносятся в сердечник как порошки и ферросплавы.
Стабилизирующие. Элементы с небольшим ионизирующим потенциалом, за счет которых при разных сварочных режимах обеспечивается устойчивая электродуга.
Газообразующие: древесная мука, целлюлоза (органические), кальцинированная сода, мрамор (металлы щелочного-земельного ряда и щелочные карбонаты). Они нужны для того, чтобы в сварочной области образовывалась газовая фаза, которая предохраняет металл в жидком виде от водорода и азота, а также с целью вытеснения с поверхности ванны воздуха.
Легирующие: порошок никеля, хрома, феррованадий, феррохром и другие. Легирующие компоненты придают нужные характеристики металлу шва.
Шлакообразующие: оксиды металлов щелочного ряда, магнезит, алюмосиликаты, кремнезем, фториды, другие руды и минералы или их сочетания.
Специальные. Чаще всего вводится железо в виде порошка, которое выполняет задачу по дополнительному влиянию на наплавочный или сварочный процесс.
Стоит сказать, что по виду наполнителя порошковая проволока для полуавтомата причисляется к одному из пяти типов. Они бывают: рутил-флюоритными, флюоритными, рутил-органическими, рутиловыми и карбонатно-флюоритные. Чаще всего применяются изделия с серденчиками последнего из перечисленных типов.
Принципы классификации порошковых проволок для сварки
Классификация таких изделий производится по:
Типу сердечника;
Возможности выполнения работ в разных положениях сварочного электрода;
Основному назначению;
Механическим характеристикам;
Варианту используемой защиты.
Самой значимой признается классификация по механическим характеристикам соединения и металла шва, так как она позволяет четко установить целесообразность применения проволоки конкретной марки для сваривания заданного изделия или конструкции. Принцип такой классификации базируется на вычислении двух требуемых показателей для металла шва – ударной вязкости и сопротивления разрыву, которые определяются при проведении исследований стандартных образцов.
По пространственному положению сварочного процесса проволоки делят на те, которые используются:
В любых положениях (маркировка – "Т");
Для сварки вертикальных ("Ву") и горизонтальных ("Вх") швов;
В нижнем, вертикальном и горизонтальном положении ("В");
В горизонтальном и нижнем положении на вертикальной плоскости ("Н").
Также широко распространена классификация порошковой проволоки для полуавтомата по ее типу:
Самозащитная (ПС);
Требующая добавочной защиты сварочной ванны (ПГ).
При использовании ПГ-проволоки ванну дополнительно предохраняют флюсом либо смесью газов. А вот ПС-изделия можно применять без всех этих ухищрений, усложняющих сварочный процесс. Когда эксплуатируется самозащитная проволока, ванна предохраняется за счет расплавления и диссоциации шлако- и газообразующих материалов, имеющихся в проволочном электроде.
Особенности производства порошковой проволоки
Изготовление порошковой проволоки для полуавтомата осуществляется в четыре этапа. Сначала подготавливается шихта и стальная лента, затем производится формирование профиля и последующая навалка на него шихты. За этими операциями следует операция волочения. На финальной стадии выполняют контроль качества полученного изделия.
Ленту подготавливают так:
Берут рулон стального материала (его ширина обычно варьируется в пределах 10–15 сантиметров);
Разрезают заготовку на спецагрегате на требуемые по ширине полосы;
Наматывают получившиеся полосы на кассеты (при этом сразу выполняется и удаление с полосок влаги, остатков смазки);
По определенной рецептуре подготавливают шихту, а затем направляют ее в виде однородной композиции на волочильный стан (к его засыпному механизму).
На следующем этапе производства порошковой проволоки шихту засыпают на ленту (процесс производится в особых формующих емкостях), из получившейся смеси формуют профиль (круглый), который начинают протягивать на волочильных барабанных агрегатах. Причем таких агрегатов имеется шесть. На каждом последующем сечение исходной заготовки уменьшается на заданную величину. В результате, на финальном барабане проволока получает требуемый по техусловиям диаметр. Заметим, что для снижения себестоимости готовой продукции и повышения уровня ее производительности процесс волочения ведется на достаточно больших скоростях (не менее 300 метров в минуту).
Под контролем проволоки после волочильного оборудования подразумевают, прежде всего, расчет особого коэффициента, который является отношением веса шихты на единицу длины проволоки к общему весу изделия. Данную величину называют коэффициентом заполнения. Для разных марок порошковой проволоки он свой (варьируется от 25 до 40 процентов). Кроме этого, проволока проходит обследование на механические показатели наплавленного металла и на свои сварочно-технологические характеристики.
Описание популярных марок порошковых проволочных изделий
Многие сварочные работы на строительных объектах выполняются вертикальными швами. Для проведения подобных мероприятий предназначены изделия ПП-АН11 и ПП-АН7. Производство порошковой проволоки данных марок осуществляется из стальной ленты 0,18 миллиметров (толщина заготовки).
В шихту для АН7 и АН11 добавляют элементы, которые дают возможность получать быстро кристаллизующийся шлак. Он помогает сварочной ванне держаться в вертикальной плоскости достаточно долгое время, вплоть до полного завтердевания шва. При использовании описываемых марок ПП рекомендуется подавать ее со скоростью около 120 метров в час, применяя сварочный ток в пределах от 130 до 170 ампер.
Проволоки ПП-АН19 и ПП-АН24 по многим технологическим особенностям идентичны изделиям, рассмотренным выше. Но АН19 и АН24 дают больше шлака, что улучшает защиту сварочной зоны (правда, при этом сама сварка становится более трудной для исполнителя). За счет "излишков" шлаковой массы такие проволоки гарантируют стабильные механические показатели соединения. Обычно их применяют для сварки конструкций, в которых шов меняет свое расположение от потолочного до нижнего (например, в трубопроводах).
Стыки различных трубопроводов также нередко завариваются проволокой марки ППТ-7. Делают ее из ленты 0,3 миллиметра. В шлаке такого электрода имеется двуокись циркония, которая прекрасно защищает от поступления азота сварочную зону. При использовании ППТ-7 сварные соединения характеризуются отсутствием чешуек на шве, характерным блеском и уникальной гладкостью. По рекомендуемым режимам выполнения сварочных мероприятий эта проволока похожа на ПП-2ДСК, которая создана для работы в нижнем положении.
ПП-2ДСК применяется на токе от 200 до 450 ампер, подается она со скоростью до 337 метров в час (минимум – 100 метров), а на электродуге присутствует напряжение от 23 до 31 вольт. Особенность шихты для этого изделия состоит в наличии в ней большого количества (свыше 50 процентов) плавикового шпата, а также алюминиевого порошка. За счет такого состава шлак после сварки можно без малейших затруднений удалить со шва.
Для сварки в автоматическом режиме в большинстве случаев применяется ПП-2ВДСК, которая имеет сложную шихтовую композицию, направленную на то, чтобы шлак, формирующийся при плавлении проволоки, помогал максимально полно удалять нитридные и оксидные соединения из жидкого металла. Это очень важно, так как именно в них в связанном состоянии находится кислород и азот воздуха. Основным компонентом шихты для ПП-2ВДСК является никель.
Видео
В сюжете - Сварка полуавтоматом без газа
В сюжете - Какую порошковую проволоку купить
В сюжете - Плюсы и минусы работы с порошковой проволокой
В сюжете - Как заправить порошковую проволоку в полуавтомат
В продолжение темы посмотрите также наш обзор Сварка алюминия полуавтоматом — особенности, требования к оборудованию, технология
Источник
https://santekhnik-moskva.blogspot.com/2021/07/Sam...ovoloka-dlya-poluavtomata.html
https://dzen.ru/media/masteronlayn/vyzov-santehnika-perovo-60c6390ae72f9332f7bb9dd2
https://santekhnik-moskva.mirtesen.ru/blog/43533216078/Perovo-REMONT-SANTEHNIKI
https://santekhnik-moskva.blogspot.com/p/v-moskve.html
https://tvin270584.livejournal.com/940834.html
https://dzen.ru/media/masteronlayn/vyzov-santehnik...oskvy-63e5bb9971cd82100dd21989
https://santekhnik-moskva.mirtesen.ru/blog/4338897...yone-Moskvyi-REMONT-SANTEHNIKI
Антон_Росляков
Суббота, 03 Сентября 2023 г. 01:26 (ссылка)
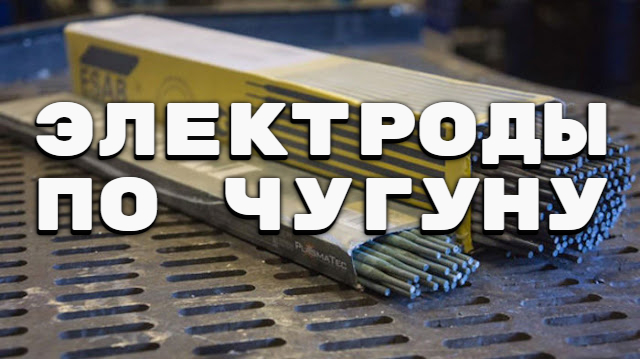
В процессе строительства и ремонта приходится работать с разными материалами, среди которых немало чугунных изделий. Как известно, чугун «капризный» сплав, сварка которого возможно только при соблюдении правильной технологии (наиболее распространенные - наплавка, горячая и холодная сварка) и, конечно, с использованием специальных электродов по чугуну. Учитывая какой вид чугуна (высокопрочный, серый, белый или ковкий), используют соответствующие электроды. В этой статье мастер сантехник расскажет, какими электродами варить чугун.
Основные сложности процесса
Сложность сварки чугуна объясняется в первую очередь химической структурой и свойствами этого материала. Чугун, как известно, является сплавом, содержащим железо и углерод, в составе которого дополнительно присутствуют как примеси (сера, фосфор, марганец, кремний), так и легирующие добавки (хром, алюминий, магний, ванадий, никель и др). Те марки данного металла, которые не содержат легирующих добавок и не подвергаются термической обработке, отличаются невысокой прочностью и твердостью. Детали из такого металла, кроме того, очень хрупкие.
Плохая свариваемость чугуна объясняется целым рядом факторов.
К ним относятся следующие:
В сварочной ванне происходит окисление различных элементов, в том числе и кремния, в результате на ее поверхности образуются тугоплавкие оксиды. По причине своей тугоплавкости такие оксиды приводят к образованию в зоне соединения непроваренных участков.
Место соединения охлаждается очень быстро, и в структуре металла образуется цементит, который отличается повышенной твердостью. Участки металла с цементитной структурой, которые называются отбеленными, очень сложно поддаются дальнейшей механической обработке.
Чугун относится к категории жидкотекучих материалов, в расплавленном состоянии из него очень сложно сформировать соединение и удержать металл в его зоне. Если посмотреть на видео процесса сварки чугуна, то заметно, как металл буквально вытекает расплавленными ручейками из-под электрода.
При осуществлении сварочных работ с чугуном необходимо обеспечивать равномерный нагрев, а также охлаждение деталей. Если пренебречь этими требованиями, то велик риск появления трещин в зоне соединения.
В расплавленном состоянии такой материал, как чугун, склонен к активному выделению газов, что приводит к пористости сварного шва.
Выполнение сварки чугуна электродами
Технология сварки чугуна предполагает использование угольных или покрытых электродов для чугуна, применение инверторов, а также газосварочных аппаратов. Если для сварки чугунных деталей используется газовая горелка, то для формирования шва применяется присадочный материал.
По типу формируемого шва технологии сварки чугуна разделяют на три категории:
Сварочный шов формируется с использованием цветных металлов, а также их сплавов;
Для получения шва используется низкоуглеродистая сталь;
Шов формируется из чугуна.
По способам предварительной подготовки деталей технологии сварки чугуна бывают:
Без предварительного нагревания деталей (так называемая холодная сварка);
С предварительным нагревом деталей до 450 градусов;
С предварительным нагревом до 650 градусов.
Подогрев чугунных деталей перед сваркой позволяет защитить их от появления участков с отбеленным металлом и минимизировать риск возникновения трещин в зоне соединения. Данная технология позволяет придать чугуну в области сварного шва те же характеристики, что и у основного металла. Холодная технология востребована в тех случаях, когда шов формируется за счет использования электродов, стержни которых изготовлены из цветных металлов или стали.
Процентное содержание элементов в электродах из чугуна марки А и Б
При предварительном подогреве применяют электроды, изготовленные из чугуна (марки «А» и «Б»). Работы выполняются на токах с большим значением и в непрерывном режиме, что очень важно иметь в виду. Даже если необходимо выполнить большой объем работ по сварке одной конструкции, то они не прекращаются, что обеспечивается за счет задействования нескольких специалистов, работающих посменно.
Кроме этого, электроды для сварки чугуна могут быть и угольными с диаметром стержней от 8 до 20 мм. В таком случае работы выполняются на токе прямой полярности, а руки сварщика защищаются от теплового излучения специальным щитком, закрепленным на держателе.
Хотя технология горячей сварки и является безальтернативной во многих ситуациях, она имеет ряд существенных недостатков. К ним, в частности, относятся:
Высокая стоимость технологического процесса;
Его продолжительность по времени;
Трудоемкость работ по выполнению такой сварки (так как требуется равномерный нагрев всей поверхности деталей и формовка мест соединения).
Виды электродов для сварки чугуна
Электроды, используемые для соединения деталей из чугуна, классифицируются в первую очередь в зависимости от материала, из которого выполнен их стержень. Такими материалами могут быть:
Проволока, изготовленная из легированных сталей;
Сварочная проволока из углеродистой стали;
Прутки, выполненные из чугуна;
Медная проволока (или выполненная из сплавов этого металла).
Электроды по чугуну, изготовленные из стали, покрываются специальным составом, который в обязательном порядке содержит ферросилиций. Использование такой присадки в обмазке электрода дает возможность получить сварочный шов, состоящий из серого чугуна. Как правило, такие электроды применяются для сварки несложных деталей, которые не испытывают серьезных нагрузок при эксплуатации.
Такими электродами нередко выполняется сварка чугуна также и в домашних условиях. Прежде чем выполнять такую сварку, лучше всего посмотреть обучающее видео, что даст возможность ознакомиться с основными нюансами процесса. Опытный специалист может получить плотный и надежный шов даже при помощи таких электродов.
Электроды, которые изготавливаются из стальной проволоки, имеют маркировку Св-08 и Св08А. Кроме этого, используются электроды следующих марок:
ЭМЧС — электроды с сердечником из низкоуглеродистой стали. Многослойное покрытие таких электродов выполняет одновременно несколько функций: защищает зону сварки, образует газ, формирует шлак и легирует металл шва. При применении таких электродов нет необходимости в предварительном нагреве деталей из чугуна. Между тем использование таких электродов для чугуна возможно лишь для соединения деталей, толщина которых не превышает 10 мм.
ЦЧ-4 — наиболее распространенный тип электродов, используемых для соединения деталей, изготовленных из чугуна. Покрытие таких электродов содержит в своем составе компоненты, которые активно вступают в химическую реакцию с углеродом, в результате чего образуются карбидные соединения, не растворяющиеся в железе.
МНЧ-1 — электроды, стержень которых изготовлен из монель-металла, представляющего собой сплав никеля (60–70%) и меди (25–30%). Сварочный шов, сформированный из такого металла, характеризуется повышенной устойчивостью к образованию трещин и обладает хорошей обрабатываемостью. Кроме того, такие электроды способствуют графитизации металла шва, а также уменьшают в нем количество растворенного углерода, что минимизирует риск формирования цементитной структуры (отбеливания).
Электроды, стержни которых изготовлены из чугуна. Такие электроды выпускаются с покрытиями двух типов. Первые из них состоят из смеси углекислого бария (24%) и карборунда (55%), которые соединяются жидким стеклом. Второй тип обмазки изготавливается из компонентов графитообразующей группы.
Электроды для сваривания чугуна также изготавливаются и из стержней комбинированного типа. В частности, это могут быть:
Стержни из сплава железа и меди, в качестве их покрытия используется специальная смесь УОНИ-13, соединенная с железным порошком;
Стержни, состоящие из одного или двух медных прутков, соединенных в пучок со стальной проволокой;
Медные электроды с жестяной оплеткой.
Решая вопрос, какими электродами воспользоваться, следует учитывать как характеристики металла деталей и их геометрические характеристики, так и требования, которым должны удовлетворять готовые соединения. В процессе электросварки следует придерживаться всех требований и правил безопасного проведения сварочных работ.
Видео
В сюжете - Как правильно сваривать чугун и какие электроды выбрать
В сюжете - Сварка чугуна по лёгкому
В сюжете - Как сделать электроды своими руками для сварки чугуна
В продолжение темы посмотрите также наш обзор Почему липнет электрод при сварке
Источник
https://santekhnik-moskva.blogspot.com/2019/04/Elektrody-po-chugunu.html
Антон_Росляков
Воскресенье, 13 Августа 2023 г. 09:45 (ссылка)

В сварочном ремесле умение правильно выбирать электроды в зависимости от типа соединений и марки стали — очень важный профессиональный навык. В этой статье мастер сантехник расскажет вам об основных разновидностях электродов для сварки инвертором.
Как работают и чем отличаются
Электрод — простой металлический стержень, который плавится в зажженной электрической дуге и заполняет собой шов между двумя деталями, попутно разогревая их кромки. Покрытие электрода, сгорая, ионизирует среду и поддерживает непрерывное горение дуги. К тому же, при сгорании состав выделяет газы, вытесняющие кислород из сварочной ванны, и образует шлак, который всплывает на поверхность расплавленного металла и накрывает его, защищая от коррозии, растрескивания и прочих негативных эффектов в момент остывания.
Понимание сути работы электродов очень важно для объяснения такого огромного количества их разновидностей. Различаются они не только по прочностным характеристикам шва, но также по его положению и типу используемого сварочного тока.
Критерии выбора электродов
Выбирая электроды для сварки с использованием инвертора, следует учитывать то, что материал изготовления соединяемых деталей также будет оказывать влияние на качественные характеристики формируемого шва. Соответственно, для того чтобы варить разные материалы, используются сварочные электроды разных типов. Так, к примеру:
Для соединения изделий, выполненных из низкоуглеродистых и низколегированных марок сталей, выбирают углеродные электроды;
Для соединения изделий, выполненных из легированных сталей, используют электроды соответствующих марок: ОЗС-4, МР-3 (ГОСТ 9466-75), МР-3, АНО-21, УОНИ 13/45 (ГОСТ 9467-75);
Если необходимо выполнять сварочные работы с наплавками или сталями других типов, то выбирают электроды с сердечником из высоколегированного металла — ЦЛ-11 (ГОСТ 9466-75);
Для того чтобы варить чугун, тоже необходимо выбрать электроды соответствующей марки — ОЗЧ-2 (ГОСТ 9466-75).
На сегодняшний день сформировался следующий рейтинг электродов, применяемых для сварки с использованием инвертора:
АНО. Сварочные электроды данной марки хорошо воспламеняются, их не надо дополнительно прокаливать. С ними одинаково успешно могут работать как начинающие сварщики, так и профессионалы.
МР-3 — универсального типа, их можно использовать даже для соединения неочищенных поверхностей.
МР-3С. Электроды данной марки следует выбрать, если к характеристикам шва предъявляются повышенные требования.
УОНИ 13/55 используют для монтажа ответственных конструкций, требующих высокого качества исполнения сварного шва. Начинающему сварщику с ними работать будет сложно: их использование требует определенного опыта и высокой квалификации.
Преимущества популярных марок электродов
Многие современные виды электродов для сварки с использованием инвертора обладают следующими преимуществами:
Простота выполнения сварки. Сложности при сварке такими электродами могут возникнуть, если вы некорректно подобрали их по составу материала сердечника.
Высокое качество шва. Данный параметр является самым важным при сварочных работах, и электроды указанных марок позволяют его обеспечить. Используя такие электроды для инвертора, можно получать качественные внутренние и наружные соединения, сварные швы выпуклой и вогнутой формы.
Легкая отделяемость шлака. Шлак, полученный при сварке с использованием таких электродов, легко отделяется, что дает возможность сразу посмотреть, какое качество шва они обеспечивают.
Можно варить детали, подвергнутые коррозии. Конечно, изделия, покрытые слоем ржавчины, варят очень нечасто, но данные электроды позволяют получить качественный и надежный шов даже в этом случае.
Процесс сварки безопасен для сварщика с точки зрения санитарно-гигиенических норм.
Различия электродов по маркам и диаметру
Среди опытных специалистов-сварщиков бытует мнение, что при использовании инвертора можно варить любыми электродами. Как правило, такое мнение основано лишь на личном опыте таких специалистов, занимающихся выполнением работ определенного типа (сварка конструкций из профильных труб или уголков). При выполнении работ с использованием инвертора к соединению не предъявляют серьезных требований по его герметичности, поэтому без проблем можно использовать электроды диаметром 0,5–2 мм.
Выбор диаметра и марки электрода должен основываться на том, какой толщины металл необходимо соединить с их помощью. Детали большой толщины требуют длительной проварки, соответственно, и электрод для их сварки необходимо подобрать большего диаметра. Сварочными электродами небольшого диаметра надо еще научиться работать, они очень быстро сгорают. Обычно такими изделиями выполняются прихватки.
На то, какие электроды лучше выбрать, оказывает влияние и тип работ, для которых их планируется использовать. Так, для выполнения сложных трассовых работ, необходимо подобрать электроды большого диаметра, а монтаж конструкций из профильных элементов можно выполнять изделиями диаметром до 2 мм. Именно такие электроды используются, в частности, при монтаже секционных ворот и изготовлении различных ограждающих конструкций из профильных труб и профнастила.
Классификация сварочных электродов
В первую очередь сварочные электроды разделяют на отдельные типы по их основному назначению. Так, принято выделять следующие типы:
Те, которыми варят углеродистые и низколегированные стали;
Для соединения конструкций из высокопрочных теплоустойчивых сталей;
Для работы с высоколегированными сталями (их часто называют «электродами по нержавейке»);
Те, с помощью которых выполняют сварку алюминия, а также его сплавов;
Предназначенные для сварки меди и ее сплавов;
Для соединения деталей из чугуна;
Те, с помощью которых производят наплавку и выполняют различные ремонтные работы;
Предназначенные для соединения деталей из сталей неопределенного состава и трудносвариваемых сталей.
На сварочные электроды могут наноситься различные покрытия. В соответствии с типом покрытия, их подразделяют на 4 категории. Самыми распространенными являются электроды с покрытиями двух типов.
Изделия с основным покрытием, которые так и называются — основными. Наиболее популярными являются изделия УОНИ 13/55. Выбрать их стоит, если необходимо получить сварные швы, соответствующие высокому качеству, отличающиеся исключительной ударной вязкостью, пластичностью и механической прочностью. Кроме этого, сварные швы, полученные при работе с такими электродами, отличаются высокой устойчивостью к возникновению кристаллизационных трещин. Также они не склонны к естественному старению. Их выбор стоит делать, если вам необходимо выполнить монтаж ответственных конструкций, которые планируется эксплуатировать в суровых условиях.
Есть у них и недостаток: если их покрытие увлажнено или на краях деталей, которые соединяются, присутствует ржавчина, следы масла или окалина, то в сварном шве формируются поры. Поры в шве могут образоваться и тогда, когда сварка выполняется на длинной дуге. Минусом использования таких электродов является и то, что ими допускается работать только на постоянном токе и обратной полярности.
Второй тип — электроды с покрытием рутилового типа. Изделия с таким покрытием, наиболее популярной маркой которых является МР-3, успешно используются для соединения деталей, материалом изготовления которых является низкоуглеродистая сталь. Сварочные электроды данной марки отличаются следующими технологическими преимуществами:
Устойчивое горение дуги при работе как на постоянном, так и на переменном токе;
Минимальное разбрызгивание материала в процессе выполнения сварки инвертором;
Возможность получать качественные сварные швы любого пространственного положения;
Легкая отделяемость шлака;
Сварные швы отличаются прекрасными декоративными характеристиками;
Подходят для сваривания поверхностей, покрытых ржавчиной или загрязнениями.
Выбор изделий в соответствии с другими параметрами
Род тока, а также полярность его подключения являются важнейшими параметрами сварочных операций. Сварочные инверторы преимущественно вырабатывают постоянный ток, который может подключаться к заготовке и электроду по двум схемам.
Прямая полярность. При такой схеме плюс подключают к массе, а минус — к сварочному электроду.
Обратная полярность. Такая схема предполагает подключение минуса к массе, а плюса, соответственно, к держателю с электродом.
Если варить инвертором на прямой полярности, то соединяемые поверхности подвергаются значительному нагреву, чего не происходит при подключении полярности по обратной схеме. Именно поэтому выбор обратной полярности целесообразен в следующих ситуациях.
При выполнении сварки инвертором деталей небольшой толщины. Обратная полярность в таких случаях поможет защитить матриал от прожога.
На обратной полярности выполняется сварка деталей, выполненных из высоколегированных сталей, которые очень чувствительны к перегреву.
Прямую полярность, при использовании которой заготовка подвергается значительному нагреву, оптимально использовать для соединения материалов, отличающихся большой толщиной и массивностью.
При выполнении любых сварочных работ с использованием инвертора наиболее значимыми являются три параметра, которые взаимосвязаны друг с другом:
Сила сварочного тока;
Диаметр электрода;
Толщина соединяемых деталей.
На выбор электродов толщина соединяемых деталей оказывает непосредственное влияние. При необходимости соединения тонких деталей (до 1,5 мм), ручная сварка не используется, для этой цели лучше подойдут полуавтоматические аппараты или же устройства, позволяющие выполнять сварку в защитной среде аргона.
Решая, какие электроды выбрать для сварки конструкций определенной толщины, можно руководствоваться следующими критериями:
Для деталей, толщина которых составляет 2 мм, лучше всего подойдут электроды Ø 2,5 мм;
При соединении деталей толщиной 3 мм, следует выбирать электроды Ø 2,5–3 мм;
Если толщина свариваемых деталей составляет 4–5 мм, то подойдут электроды Ø 3,2–4 мм;
Детали толщиной 6–12 мм лучше всего варить электродами Ø 4–5 мм;
Когда толщина превышает 13 мм, то оптимальным будет выбор электродов Ø 5 мм.
Правильно выбирать диаметр электродов очень важно, так как при превышении этого параметра снижается плотность сварочного тока. Это приведет к тому, что сварочная дуга станет неустойчивой, ухудшится провар деталей, увеличится ширина сварного шва. Многие производители указывают на упаковке информацию о том, какие значения силы тока лучше всего использовать.
Если же такой информации на упаковке не содержится, то можно руководствоваться следующими рекомендациями:
Для сварки электродами Ø 2 мм следует устанавливать сварочный ток, сила которого составляет 55–65А;
Для изделий Ø 2,5 мм используют ток 65–80А;
Электроды Ø 3 мм — ток 70–130А;
Для электродов Ø 4 мм выбирают сварочный ток 130–160 А;
Изделия Ø 5 мм — ток 180–210 А;
6-ми миллиметровыми электродами лучше варить на токе 210–240 А.
Как становится понятно из всего вышесказанного, для качественной сварки инвертором важен правильный выбор электродов по их диаметру. Также следует устанавливать оптимальную силу сварочного тока. Если, к примеру, вы соберетесь варить инвертором тонкий металл, используя электроды большого диаметра, или сила сварочного тока будет превышать допустимые значения, то в готовом шве могут образоваться поры, что значительно снизит его качественные характеристики.
Электроды зарубежных производителей
На отечественном рынке большую популярность завоевали электроды торговой марки ESAB. Характерной особенностью электродов от шведского производителя является то, что их маркировка начинается с обозначения «ОК», за ним следуют 4 цифры. Среди большого разнообразия моделей электродов данной торговой марки наибольшее распространение получили следующие из них.
ОК 46.00. По характеристикам они очень похожи на отечественные изделия МР-3. Ими с применением инвертора можно варить углеродистые, низколегированные стали, используя постоянный, а также переменный ток. При их использовании обеспечивается высокое качество получаемого соединения.
ОК 48.00. Работать ими можно исключительно на постоянном токе, их используют для монтажа особо ответственных конструкций.
ОК 53.70. Относятся к специализированному типу, с их помощью выполняют сварку корневых проходов, соединения стыков труб.
ОК 61.30 и 63.20. Их используют для сварки инвертором деталей из нержавеющей стали, но перед их приобретением важно уточнить, подойдут ли они для работы с интересующей вас маркой металла.
ОК 68.81. При помощи изделий данной марки выполняют сварку инвертором деталей из неопределенных марок сталей, а также из трудносвариваемых марок.
ОК 96.20. Ими работают по чугуну, а также соединяют чугунные детали со стальными.
ОК 92.60. Предназначены для сварки изделий из алюминия, его сплавов с использованием инвертора.
К слову сказать, в ассортименте электродов данной торговой марки есть и изделия, которыми можно выполнять сварку меди и ее сплавов.
Чем руководствоваться при выборе электродов
Резюмируя все вышесказанное, можно выделить ряд основных параметров, на основе которых следует выбирать электроды для инверторной сварки. В первую очередь необходимо учитывать тип материалов, которые вы собираетесь варить. Если требуется монтаж ответственной конструкции, то лучше выбрать для этого электроды от хорошо зарекомендовавшего себя производителя. К примеру, для таких целей хорошо подойдут изделия торговой марки ESAB, выпускаемые известным шведским производителем.
Если поверхность деталей из углеродистых сталей, которые вы собираетесь варить инвертором, покрыта ржавчиной или влажная, то лучше выбирать электроды с покрытием рутилового типа.
Изделия с основным покрытием используют в тех случаях, если необходимо выполнить сварку инвертором особо ответственных конструкций. Качество сварки такими электродами зависит и от того, насколько тщательно вы подготовили соединяемые поверхности. Чтобы понять, как выполняется такая подготовка, можно посмотреть обучающее видео, которое несложно найти в интернете.
От того, какой толщины детали вам необходимо варить инвертором, зависит не только выбор диаметра электрода, но и силы сварочного тока, который также оказывает влияние на качество формируемого соединения.
При планировании сварочных работ всегда следует помнить, что правильно подобранные электроды позволят вам получить качественное соединение даже в том случае, если вы используете в работе недорогой инвертор.
Видео
В сюжете - Как выбрать электрод для сварки
В сюжете - Как расспознать тип электродов и понять для чего они применяются
|